半導体の前工程・後工程とは?それぞれの違いについても解説
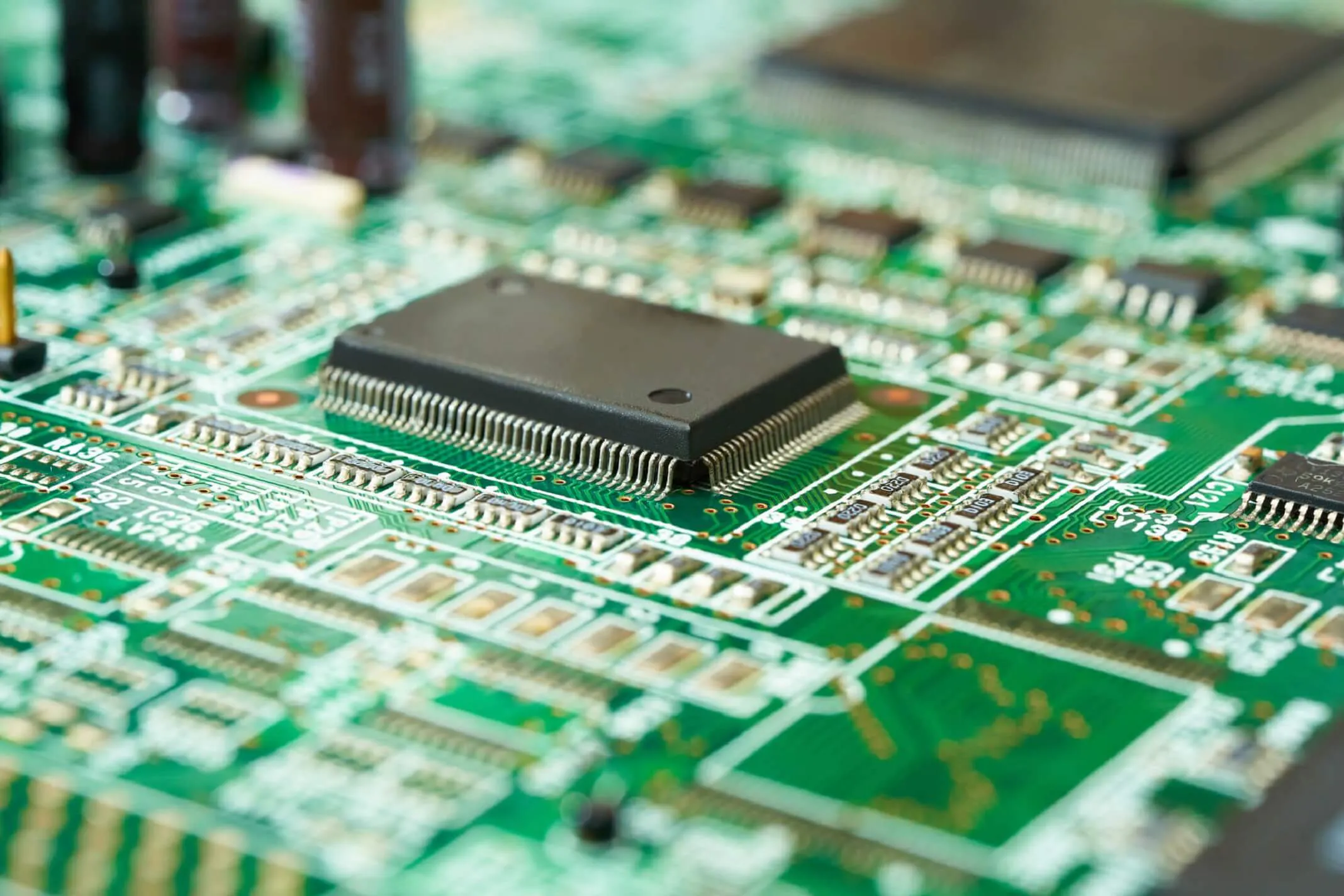
スマートフォンやパソコン、テレビなど、私たちの生活には電子機器があふれています。これらの機器の中で重要な役割を果たしているのが半導体です。
しかし、この半導体がどのように作られているのか、知っている人は少ないのではないでしょうか。半導体の製造には、「前工程」と「後工程」という2つの重要な工程があります。
この記事では、2つの工程の内容や違いついて、初めて聞く方にもわかりやすく解説していきます。
【関連記事】半導体とは?定義や仕組みをわかりやすく解説!3つの役割や日常生活での使用例も紹介
半導体の製造過程大きく分けて3種類
半導体の製造工程は、大きく3つに分けられます。
- 設計工程
- 前工程
- 後工程
設計工程は、半導体の回路設計とフォトマスクの製造を行う工程です。フォトマスクとは、回路のパターンが描かれた原版のようなもので、これを使って実際の回路を形成していきます。
次の前工程では、シリコンでできた円盤状のウェハーに、数百個の半導体チップを同時に作り込んでいきます。この工程は、ナノメートル単位の極めて精密な加工が求められ、最先端の技術が集約されている点が特徴です。
最後の後工程では、前工程で作られた半導体チップを一つ一つ切り分け、それらをパッケージングして最終的に製品としての半導体を完成させていきます。チップの保護や外部との接続など、実用化に向けたプロセスが主となる工程です。
この記事では特に、実際の製造現場で行われる「前工程」と「後工程」に焦点を当て、その特徴や違いを解説します。
【関連記事】半導体の製造工程を大公開!働く際の注意事項についても解説
半導体の前工程とは
前工程は、シリコンウェハー上に電子回路を形成する重要な工程です。
具体的には、以下のような流れで作業が行われます。
| 工程名 | 内容 | 目的 |
---|---|---|---|
1 | 表面の酸化 | 高温の酸素を数時間当て続ける | 絶縁用の酸化皮膜の形成 |
2 | 薄膜形成 | スパッタ装置やCVDによる成膜 | 回路の基礎となる薄膜の形成 |
3 | フォトレジスト塗布 | 感光剤を均一に塗布 | 回路パターン形成の準備 |
4 | 露光・現像 | フォトマスクを通して光を照射 | 回路パターンの焼き付け |
5 | エッチング | 薬品で不要部分を溶かす | 回路パターンの形成 |
6 | レジスト剥離・洗浄 | 薬品で感光材を除去 | 不要物の除去 |
7 | イオン注入 | シリコンにイオンを注入 | 電気特性の付与 |
8 | 平坦化 | 表面の研磨 | 凹凸の除去 |
9 | 電極形成 | 金属配線の埋め込み | 電気的接続の形成 |
10 | 検査 | プローブによる動作確認 | 品質の確認 |
前工程は半導体の性能を左右する重要な工程です。
特に「フォトレジスト塗布」から「平坦化」までのプロセスは、必要に応じて何度も繰り返し行われ、複雑な回路を形成していきます。各工程では、さまざまな環境条件を厳密に管理する必要があり、ナノメートル単位の精度が要求されるため、高度な技術と最先端の製造装置が欠かせません。
半導体の後工程とは
後工程は、前工程で形成された回路を実際に使える製品へと仕上げる工程です。
チップの保護や外部との接続など、半導体の実用化に向けた役割を担っており、以下の4つのステップがあります。
| 工程名 | 内容 | 目的 |
---|---|---|---|
1 | ダイシング | ウェハーを個々のチップに切断 | 個別チップへの分割 |
2 | ワイヤーボンディング | リードフレームにチップを固定し配線 | 外部との電気的接続 |
3 | モールディング | 樹脂による封止 | チップの物理的保護 |
4 | 最終検査 | 電気特性や耐久性の確認 | 品質の保証 |
後工程は、前工程で作られた「半導体の心臓部」を実用的な製品へと仕上げる工程です。
「ダイシング」では、高精度な切断技術により、前工程で形成された精密な回路を損なうことなく個々のチップに分割し、「ワイヤーボンディング」では、人間の髪の毛よりも細い金線を使って、チップと外部端子を正確に接続します。
最後の検査工程では、温度変化や電気的特性などいくつもの観点から製品の品質が細かくチェックされ、厳しい検査を通過した製品のみが市場に出荷されることとなります。
半導体の前工程と後工程の違い
半導体製造における前工程と後工程は、それぞれ異なる特徴と役割を持っています。これらの違いを理解することは、半導体製造プロセス全体を把握する上でも重要でしょう。
主な違いは以下の3つの観点で整理できます。
- 製造フロー:工程の進め方や特徴
- 装置・材料:使用する設備や原材料の違い
- 求められる技術:必要とされる専門知識やスキル
これらの観点から、前工程と後工程の違いを解説します。
製造フロー
前工程と後工程では、製造の進め方が大きく異なります。
前工程は、一枚のウェハーに対して同じ作業を何度も繰り返す「サイクル型」の製造フローです。例えば、トランジスタ層や配線回路層の形成では、成膜、パターン転写、エッチングという一連の作業を、層の数だけ繰り返します。
一方、後工程は「直線型」の製造フローです。切断から始まり、配線、封入、検査という順序で、一方向に作業が進んでいきます。各工程は一度きりで、やり直しがきかないため、高い精度と安定性が求められます。
また、前工程が一枚のウェハーを扱うのに対し、後工程では個々のチップを扱うため、作業の管理方法も異なります。
装置・材料
前工程と後工程では、使用する装置や材料にも違いがあります。
前工程で使用される装置は高価で、最新の露光装置は1台で100億円を超えることもあります。この露光装置は、ナノメートル単位の微細な回路パターンを正確に転写するために、高度な光学系と精密な制御システムを備えています。
その他にも、エッチング装置や成膜装置など、クリーンルーム内に設置される装置のほとんどが高額な専用機です。材料面でも、超高純度のガスや特殊な化学薬品など、厳密な品質管理が必要な材料を多用します。例えば、ウェハーの洗浄に使用される純水は、一般的な水道水とは比較にならないほど不純物が少ない特殊なものです。
一方、後工程の装置は比較的シンプルで、汎用性の高いものが多くなっています。ダイシング装置、ワイヤーボンディング装置、モールディング装置など、それぞれ専用の装置は必要ですが、前工程ほどの高額な設備は必要ありません。
使用する材料も、金線や封止樹脂など、比較的一般的な工業材料が中心です。
求められる技術
前工程では、ナノテクノロジーと呼ばれる最先端の微細加工技術が必要です。数ナノメートルという極めて小さなサイズで微細な加工を実現するには、高度な物理学や化学の知識、精密な制御技術が求められます。
また、製造環境の管理も重要です。例えば、クリーンルーム内の温度や湿度などは厳密に管理する必要があります。微細な振動や静電気、わずかな金属粒子などでさえも製品の品質に影響を与えるため、こうした要因も排除しなければなりません。
同様に後工程でも、物理学や化学の知識に加えて、緻密な作業を遂行する能力が求められます。後工程ではチップを物理的に扱う技術が中心となり、例えばワイヤーボンディングでは、微細な金線を正しく接続する技術が必要です。また、モールディングでは、樹脂の流動性や硬化特性を理解し、最適な成形条件を設定する技術が欠かせません。
半導体前工程・後工程に関するよくある質問
ここでは、半導体前工程・後工程に関してよくある質問に対してお答えします。
前工程と後工程はどちらが大変?
技術的な難しさという観点では、前工程の方が大変だといえるでしょう。
その理由は主に三つあります。
一つ目は、製造工程の数が圧倒的に多いことです。一枚のウェハーに対して同じ作業を何度も繰り返す必要があり、成膜、パターン転写、エッチングという一連の作業を、層の数だけ繰り返さなければなりません。
二つ目は、極めて高い精度が要求されることです。ナノメートル単位の加工では、わずかなズレも許されません。
三つ目は、一つのミスが全体に影響することです。前工程でのミスは、ウェハー上のすべてのチップに影響を与える可能性があります。
ただし、後工程にも独自の難しさがあります。例えば、個々のチップを物理的に扱う必要があるため、破損のリスクが高まることが挙げられます。また、一度組み立てた後は修正が困難なため、高い精度と安定性が求められる点も後工程の難しいポイントです。
前工程・後工程の国内トップメーカーは?
日本の半導体製造装置メーカーは世界市場で高いシェアを誇っており、前工程と後工程それぞれの分野で、世界をリードしている企業があります。
- 前工程
東京エレクトロンは、コータ・デベロッパー(感光剤塗布・現像装置)や成膜装置、洗浄装置など、幅広い装置で世界トップクラスのシェアを誇ります。
Screenは表面処理技術や直接描画技術、画像処理技術を得意としています。
ニコンとキヤノンは、半導体製造の中でも特に重要な露光装置の分野における高い技術力が特長的です。両社は光学技術を活かし、ナノメートル単位の微細な回路パターンを形成する装置を提供しています。
- 後工程
後工程装置では、ディスコがダイシング装置(ウェハー切断装置)で世界シェアの8割以上を占めています。
東京精密は検査・測定装置、TOWAはモールディング装置(樹脂封止装置)でそれぞれ高い技術力と市場シェアを持っています。
まとめ
半導体製造における前工程と後工程は、それぞれ異なる特徴と役割を持っています。
前工程で基本となる電子回路を形成し、後工程でそれを実際に使える製品へと仕上げる、この2つの工程が組み合わさることで、現代のデジタル社会を支える高性能な半導体が生み出されているのです。
ワールドインテックのFC事業部では、充実した教育システムを通じて、未経験者でも安心してものづくりの世界に挑戦できる環境を提供しています。
最先端の製造技術を学びながら、自分らしいキャリアを築きたい方は、ぜひ一度検討してみてはいかがでしょうか。