品質管理とは?仕事内容を紹 介
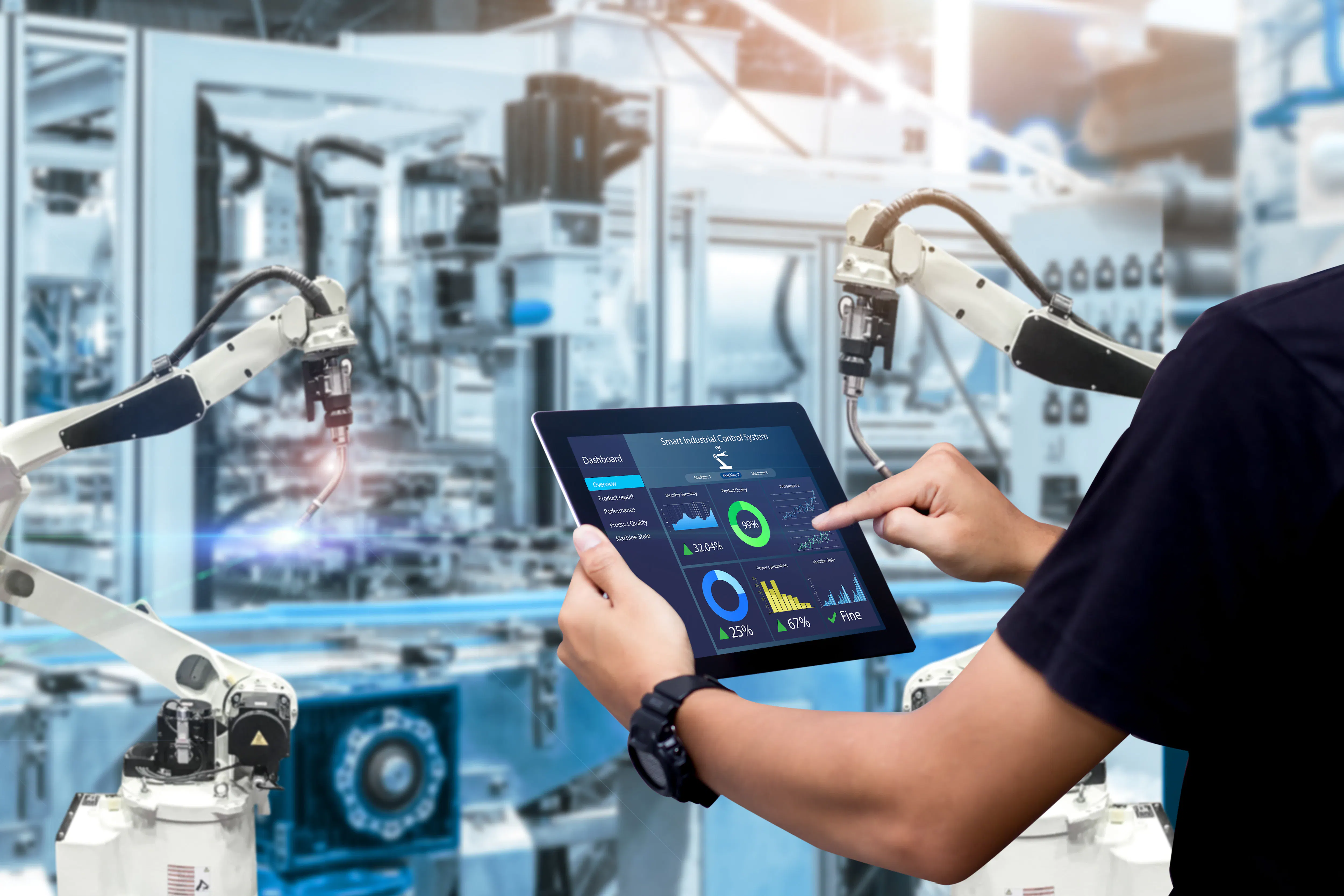
品質管理とは、製品の品質を一定に保つために様々な要素を管理することです。責任が伴いますがやりがいのある仕事です。この記事では品質管理の仕事内容や品質管理にかかわる資格について紹介しています。
品質管理の仕事に興味がある人はぜひ参考にしてください。
品質管理とは?
品質管理とは、製品の品質を検査・検証して一定水準の品質であることを保証することです。品質管理には広義と狭義の2種類があります。狭義の品質管理は「製品の品質」を管理することですが、 広義の品質管理はそれに加えて品質を保つ「製造のプロセス」まで含めて管理することを指します。今まで現場で行われてきたのは狭義の品質管理ですが、近年は「品質管理」というと広義の品質管理を指すことが一般的です。広義の品質管理は「QM(Quality Management)」、狭義の品質管理は「QC(Quality Control)」とも言われます。
品質管理は、地味で目立たない裏方的な仕事です。しかし自社製品の品質を保つという責任ある仕事です。それゆえ大きなやりがいがあり、プライドを持って取り組むことのできる仕事でもあります。
なお「品質管理」と似た言葉に「品質保証」があります。品質管理は、製品完成までの品質の管理や保証を行うものです。それに対して品質保証は、製品出荷時や納品後に顧客の満足や安心を保証するための活動です。品質管理は、品質保証の一部だと言えます。
品質管理の仕事内容は?
すでにお話したように、品質管理は製品の品質を保つ仕事です。「製品の品質を保つ」ことをもう少し細かく分けて考えると、次のように分けられます。
- 不適合品(いわゆる不良品)の発生を未然に防ぐ
- 不適合品が発生したとき対処する
- 不適合品が再発しないよう改善する
具体的な業務を通じて、これら3つを実現していきます。不適合品を未然に防ぐためには、製品の材料や製造の工程に問題がないか、部署をまたいで検査・管理することが必要です。不適合品発生の対処としては、クレーム処理などがあります。再発防止の改善には、データを分析するなどして原因の特定することが必要です。
そのため品質管理の業務には、物事を突き詰めて考えるのが得意な人・コミュニケーション能力がある人が向いています。また数字を扱うのが得意・苦手意識がないことも適性の1つです。
品質管理のやり方
品質管理のやり方としては、製品の品質を3つの側面から管理するのが基本となります。
品質管理のやり方
- 工程管理
- 品質検証
- 品質改善
品質管理の具体的な仕事は、これら3つの側面で管理することだと言えます。具体的に見ていきます。
●工程管理
製品を製造する工程を管理して品質を保つとともに、効率的に計画・運営することを言います。具体的な内容としては次の業務が挙げられます。
- 作業手順の標準化
- 品質教育・作業訓練
- 設備の維持管理
- 工程を正常に保つ管理
作業手順の標準化には、作業手順書の作成があります。作業手順書とは、皆が守るべき作業の手順や注意点をまとめたもので、作業手順を統一することによって品質を一定に保ちやすくなります。品質が一定に保たれると、異常があったときも発見しやすくなります。
品質教育・作業訓練としては、作業手順の周知徹底があります。研修やOJTの形で、標準の作業手順を習得させていきます。実際に作業を統一することが目的です。
設備の維持管理には設備の点検・修復などが挙げられます。これにより設備の不備で起こる不適合品の発生や品質のバラツキを防ぐことが可能です。さらには設備の問題が原因で作業がストップすることもなくなり、製造の効率も保たれます。
工程を正常に保つ管理としては「QC工程表」の作成・徹底があります。QC工程表は品質管理に関わる管理特性や管理方法を工程ごとに記載したものです。QC工程表を作成することにより、異常が発生したときに原因を特定しやすくなります。QC工程表は、QC工程図・QC工程管理表と呼ばれることもあります。
QC工程表をもとに、異常発生が想定される場所を洗い出します。そこに防止の仕掛けを組み込んだり、工程全体の品質確認作業をシステム化して不適合の見落としをなくす仕組み作りを行ったりします。
QC工程表は作業手順書と似ていますが、作業手順書は管理ではなく作業についてまとめたもので、内容・目的の違いがあります。
●品質検証
製品の品質を検査・検証することです。具体的には、製造工程において次の3段階での検査があります。
- 部品・原材料の受入検査
- 工程内検査
- 出荷前の検査
製造の工程が仮に完璧だったとしても、製品に使われる部品や原材料に不適合があれば製品そのものが不適合品となってしまいます。そのようなことがないように、まず部品や原材料を購入した段階で品質を検証する受入検査を行います。
さらに、製造の工程でも工程内検査を行います。不適合が発生しやすい工程や製品完成後には検査できない工程が主な対象です。工程内検査を行うことで、不適合な完成品を作ってしまうことなく、未然に防止することができるうえコスト削減にもつながります。
製品が完成したら、出荷前に最終的な検査を行います。これは完成品検査・出荷検査とも呼ばれます。機能・外観について全数検査するのが基本です。顧客からの信用度や万が一の場合の損失防止にかかわる重要な検査です。
こういった製品の検証から一歩進んで、製品の品質だけでなく、工程自体が一定の品質の製品を生産する能力があるか監視することも品質検証の一環です。工程の監視は、不適合の発生率を示す「工程能力指数」を算出・評価する方法などで行います。
さらには、それら検査や工程管理が正しく行われているかという、監視・検証自体を監視することも加わります。検査や管理そのものが決められた手順で行われているか・適切かをチェックします。ISO9000などの品質システム監査などが該当します。
●品質改善
品質の改善、不適合の未然防止、再発の防止を行うことです。製品の完成後に品質を改善することはできません。「品質改善」は製造工程における問題点を洗い出して、それをもとに今後製造される製品の品質を改善・維持することを指します。
不適合が発生してしまった場合は、現状を把握・分析して原因を明らかにし、発生原因を取り除きます。その過程で数値データの分析が必要となりますが、「QC7つ道具」などを使って問題点を絞り込んで明らかにしていきます。
不適合の未然防止のためには、工程中の不備の発見と工程の最適化を行います。検査工程そのものに不備がある場合、検査漏れが起こりうるからです。このとき現場からの言語情報を分析・改善することが多くあります。その際には、「新QC7つ道具」を使うことが有効です。
QC7つ道具・新QC7つ道具については後述します。
また、品質管理をより効率よく・不備のないように行うためには下記の手法が役立ちます。
- PDCAサイクルを回す
- データ分析を行う
- IEで脱属人的動き
1つずつ解説します。
●PDCAを回す
品質管理の業務において、「PDCA」はあらゆる場面で活用することができます。PDCAとは、4つのステップから成る継続的な業務改善の手法です。4つのステップとは次の通りです。
- Plan(計画)
- Do(実行)
- Check(確認)
- Act(改善)
PDCAは、まず計画(P)を立て、次にそれを実行(D)し、さらに結果を確認(C)し、最後に必要なら問題解決のために改善(A)する流れになっています。改善まで行ったら、問題が解決するまで計画に戻って同じステップを繰り返すのが一般的です。連続してPDCAを行うことを「PDCAサイクル」と呼び、このサイクルを繰り返すことを「PDCA(サイクル)を回す」と言うこともあります。
PDCAサイクルは、製品の品質・工程どちらが対象でも、未然防止・再発防止・改善のどれが目的であっても問題解決に有効です。PDCAサイクルを品質管理に当てはめて考えると、次のような流れとなります。
- P(計画):問題点を洗い出して解決策を立案する
- D(実行):その解決策を実行する
- C(確認):問題が解決しているか確認・分析する
- A(改善):うまく行っていない部分があればさらに改善する
問題が解決するまでこれを繰り返します。品質管理においてはこのサイクルを回すことが大切です。そして問題が解決したときにも、やりっ放しで終わらせてはいけません。解決できた手段を標準化することが必須です。必ず作業手順書やQC工程表に解決方法策を反映させます。
●データ分析を行う
現状や問題点を把握し改善していくためには、データを分析するという作業が重要になります。「QC7つ道具」を使ってデータ分析を行うと、現状や問題点を数値的・定量的に分析・可視化することができます。QC7つ道具とは次の7つです。
- グラフ
- チェックシート
- パレート図
- ヒストグラム
- 特性要因図
- 散布図
- 管理図
これらを使って分析することで、全体が俯瞰しやすくなり、問題点を理解しやすくなります。
さらに数値ではなく言語データを定性的に分析するときに役立つ手法もあります。「QC新7つ道具」と呼ばれています。言語情報を整理して問題点を浮かび上がらせるのに有効です。具体的には次の通りです。
- 親和図法
- 連関図法
- 系統図法
- マトリックス図法
- アローダイアグラム
- PDPC法
- マトリックスデータ解析法
これらを使うことで、言語データを整理し図示化・可視化することができます。それにより問題点が明らかになり、改善策が立てやすくなります。
●IEで脱属人的動き
「IE」は、工程や作業内容を科学的に分析する工程管理の手法の1つです。個人の経験や勘に頼らず、現場のムリ・ムダ・ムラをなくして最適化を行うことができます。品質管理においては、製造の実態の把握・改善・標準化に役立ちます。なお、「IE」は「Industrial Engineering(インダストリアルエンジニアリング)」の略です。
IEは2つの方法とその組み合わせとに大別できます。
- 方法研究
- 作業測定
- 組み合わせ
方法研究は、方法を最適化するために作業と作業のフローを分析することです。工程や作業方法・作業動作を細かく分析することで、作業の流れや個々の動作を改善することができます。
作業測定は、作業時間を定量的に測定・分析することです。現状の分析や評価、見積もりにも使われます。その他、非効率な作業を発見・カットするのにも役立ちます。
そして方法研究と作業測定を組み合わせた応用的な手法もあります。
品質管理の資格
品質管理の資格として「品質管理検定(QC検定)」があります。これは品質管理に関する知識を問う検定です。受験資格はとくにありません。国家資格ではないので持っていなくても品質管理の業務に携わることができますが、日常業務のための知識獲得や昇進・転職に活用できます。
難易度により1~4級の4つの級が設定されています。1級は2次試験があり、1次試験のみ合格した場合は準1級となります。レベルの目安としては、日常的な業務をこなすレベルであれば3級程度です。2級以上はマネジメントクラスの知識が求められます。
昇進や転職に役立てたいと考えるなら、2級以上の取得を目指しましょう。特に製造業においては、実務経験と2級以上の所持との両方があれば、アピールポイントになります。日常的な実務で使う知識を体系的に学びたいのなら、3級取得が目安です。
試験は毎年2回(3月・9月)に全国120箇所で実施されています。1級には対応していない開催地があります。試験はマークシート形式ですが、1級の2次試験のみ筆記形式となります。複数の級を併願することも可能です。
級ごとの合格基準・合格率は以下の通りです。
合格基準 | 合格率 (第31回 2021年3月実施) | |
---|---|---|
1級 | 以下、a.b.c.をすべて満たす場合 一次試験(手法分野、実践分野):各分野の得点が概ね50%以上であること。及び、総合得点(手法分野+実践分野)が概ね70%以上であること。 二次試験(論述):得点が概ね50%以上。 総合得点(一次・二次試験の合計点)が概ね70%以上。 | 9.18% |
2級 | 出題を手法分野・実践分野に分類し、各分野の得点が概ね50%以上であること。及び、 総合得点が概ね70%以上であること。 | 48.43% |
3級 | 52.45% | |
4級 | 総合得点が概ね70%以上 | 85.07% |
※準1級は、上記1級の合格基準のうちa.だけを満たす場合
まとめ
品質管理の業務は、不適合品の未然防止・不適合品が発生したときの対処・不適合品発生の再発防止を実現するためのものです。工程管理・品質検証・品質改善の3つの側面があり、それぞれにおいて製品の品質と製品を製造する工程とを検証・管理します。その際にはPDCAサイクル・データ分析・IEの活用が有効です。
品質管理の資格には品質管理検定(QC検定)があります。実務レベルの知識を学ぶには3級、転職や昇進に役立てたいなら2級以上の取得を目指しましょう。
品質管理は目立たない仕事ではありますが、製品の品質を管理するという会社の信用にもかかわる重要な業務です。責任があると同時に非常にやりがいのある仕事です。
興味を持たれた方はぜひ、この記事を参考にポイントなどのチェックをしてみてください。