エッチングとは表面加工技術の1つ!種類や活用分野・メリットデメリットを紹介
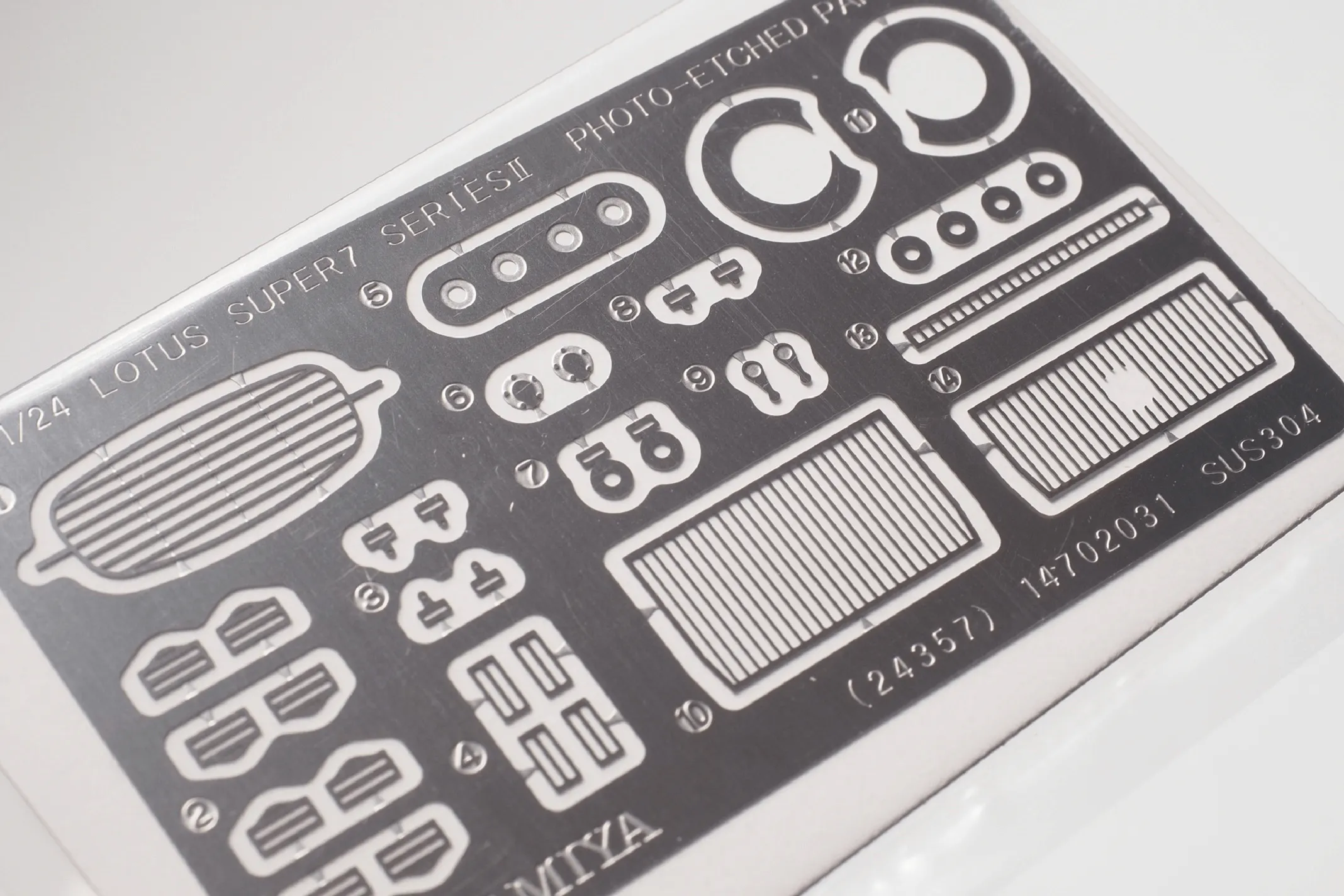
エッチングは、化学的または物理的な方法で材料表面を削り取り、微細な加工を施す技術です。半導体製造から芸術作品の制作まで、幅広い分野で活用されているこの技術は、私たちの生活に欠かせない存在となっています。
本記事では、エッチングの基本的な仕組みから、様々 な種類、産業での活用方法、そして、メリットやデメリットまで詳しく解説していきます。製造業に携わる方はもちろん、技術に興味のある方にも参考になる情報をお届けします。
エッチングとは
エッチングとは、1500年頃にヨーロッパで生まれた化学的な表面加工技術です。基本的な仕組みは、化学薬品の腐食作用を利用して材料表面を選択的に除去することにあります。特徴的なのは、加工したい部分以外を保護材で覆い、露出した部分のみを薬液で腐食させる手法を用いることです。
当初は銅版画や印刷技法として発展してきたため、金属加工での使用が一般的でしたが、現代では適切な腐食剤を選ぶことで、金属以外の素材にも応用が可能です。
また、この技術は工業的な表面加工だけでなく、金属組織の観察や検査などの分析技術としても重要な役割を果たしています。このように、芸術分野から工業、科学分野まで幅広く活用される versatile な加工技術として確立されています。
【関連記事】
半導体におけるエッチングの手法を解説!メリット・デメリットや加工の流れも紹介
ドライエッチングとウェットエッチングの2種類がある
エッチングは、加工方法によって二つの種類に分けられます。ここでは、半導体工学でも使われるドライエッチングとウェットエッチングについて解説します。
ドライエッチング
ドライエッチングは、プラズマ化したガスから生成されるイオンを利用した先進的な表面加工技術です。真空チャンバー内で電極間に高周波電力を印加してガスをプラズマ化し、発生したイオンを材料表面に高速で衝突させることで、物理的に表面原子を除去します。
このプロセスには、材料表面を全方向に均一に加工する等方向性エッチングと、垂直方向のみに選択的に加工を行う異方向性エッチングの2種類があり、用途に応じて使い分けることで、微細な加工が可能となります。
ウェットエッチング
ウェットエッチングは、酸やアルカリなどの液体状の化学薬品を用いて材料表面を溶解する加工方法です。この技術には「等方性エッチング」と「異方性エッチング」という2つの特徴的なプロセスがあります。
等方性エッチングは反応が全方向に均一に進行し、丸みを帯びた形状が特徴ですが、異方性エッチングは特定の方向に優先的に反応が進むため、シャープなエッジを形成できます。これらの特性は薬液の濃度、種類、温度などの処理条件によってコントロールされ、目的に応じた最適な条件設定には豊富な経験と技術が必要とされます。
エッチングの活用分野
エッチング加工は、さまざまな分野で活用されています。
ここではその一例を紹介します。
- フォトエッチング
- 版画・印刷
- 半導体工学
フォトエッチング
フォトエッチングは、写真技術を応用した精密な表面加工方法です。この技術では、基板に感光性のレジストを塗布し、回路パターンを光で転写した後、マスキング処理を行い、不要な部分を選択的に除去します。特に、プリント配線基板や集積回路などの電子部品の製造において重要な役割を果たしています。
微細で複雑な形状の加工が可能で、極めて薄い材料にも対応できる上、レーザー加工と比較してコスト効率が高いことが特徴です。このような利点から、エレクトロニクス産業における基幹的な加工技術として広く活用されています。
版画・印刷
版画・印刷におけるエッチングは、化学的な腐食作用を利用して銅版に図柄を刻む伝統的な芸術表現技法です。具体的には、防食材で保護された銅板の表面をニードルなどの針で描画して防食層を除去し、その後、酸による腐食作用で線や模様を刻み込みます。
このようにして作られた凹版に、インクを詰めて印刷することで、繊細な階調や豊かな表現が可能な芸術作品を生み出すことができます。このため、美術分野では「エッチング」という言葉が、この技法で制作された印刷作品自体を指すこともあります。
半導体工学
半導体工学は、電子デバイスの設計・製造に関する技術を研究する工学分野です。この分野では、微細な回路パターンを形成するために「ウェットエッチング」と「ドライエッチング」という2つの主要な加工技術が用いられます。ウェットエッチングは化学薬品を使用し、複数の基板を同時に処理できることからコスト効率が高いという特徴があります。
一方、ドライエッチングは真空環境下でプラズマなどを使用する方式で、より精密な加工が可能であり、周辺への汚染も少ないという利点があります。これらの技術は半導体デバイスだけでなく、MEMS(微小電気機械システム)の製造にも広く活用されています。
エッチング加工の対象となる材料
材料名 | エッチングの種類 | 特徴 |
---|---|---|
シリコン | ウェットエッチング ドライエッチング | 半導体材料として広く使用され、異方性エッチングにより微細な構造を作製可能 |
ガラス | ウェットエッチング | 透明性、耐薬品性に優れ、ディスプレイや光学部品に利用 |
金属 (アルミニウム、銅、金など) | ウェットエッチング ドライエッチング | 電気伝導性、熱伝導性に優れ、配線や電極に利用 |
セラミックス | ウェットエッチング ドライエッチング | 耐熱性、耐摩耗性に優れ、電子部品や構造材料に利用 |
ポリマー (樹脂) | ウェットエッチング ドライエッチング | 軽量、柔軟性、絶縁性に優れ、マイクロ流体デバイスやMEMSに利用 |
ただしエッチングの種類は、材料や用途によって異なります。また材料によっては、特殊なエッチング方法が用いられる場合があります。
エッチング加工のメリット
金属加工には、エッチングのほかにプレス加工などもありますが、エッチングならではのメリットとは何でしょうか。
エッチング加工のメリットとして挙げられるのは以下の通りです。
- 金型が不要
- 繊細な加工ができる
- 変形しにくい
金型がいらない
エッチング加工は金型を必要としないため、製造工程の簡略化とコスト削減を実現できる革新的な加工方法です。従来のプレス加工や金属加工では、製品形状ごとに専用の金型を作製する必要があり、その設計・製作には多大な時間と費用が発生していました。
しかしエッチング加工では、デジタルデータから直接製品を作製できるため、試作品の製作や少量多品種生産において優位性を持ちます。例えば、スマートフォンの内部に使用される微細な金属部品や、医療機器の精密部品などの製造において、金型製作のコストと時間を大幅に削減できます。また、製品デザインの変更にも柔軟に対応できるため、開発期間の短縮にも貢献します。
繊細な加工ができる
エッチング加工は、微細かつ精密な表面加工を実現できる技術として、特に電子機器の小型化・高性能化に貢献しています。
例えば、スマートフォンの心臓部となる半導体チップでは、髪の毛の太さの1000分の1以下という超微細な回路パターンをエッチング加工で形成することが可能です。この繊細な加工技術により、1つのチップ上により多くの電子回路を集積することが可能となり、結果として処理速度の向上やバッテリー消費量の削減といった消費者メリットにつながっています。
また、医療機器の分野でも、極めて小さなセンサーや治療用デバイスの製造にエッチング加工が活用され、より低侵襲な医療の実現に役立っています。
変形しにくい
エッチング加工は、材料に機械的な力をかけることなく化学反応で加工を行うため、材料の変形や歪みが極めて少ないという大きな利点があります。特に薄い金属板や精密部品の加工において、この特徴は重要な価値を持ちます。
例えば、スマートフォンの内部に使用される極薄の金属部品や、精密機器のコネクタなどの製造では、従来のプレス加工やレーザー加工では避けられなかった応力による変形が、エッチング加工ではほとんど発生しません。これにより、製品の寸法精度が高く保たれ、後工程での組み立て精度の向上や、製品の信頼性向上にもつながっています。
エッチング加工のデメリット
エッチング加工には、生産に適さない条件や不向きな材料があります。
エッチング加工のデメリットとして挙げられるポイントは以下の通りです。
- 大量生産には向かない
- 厚板の加工は不向き
大量生産には向かない
エッチング加工は、化学反応を利用する性質上、一回の処理に一定の時間を要するため、大量生産には適していないという制約があります。特に複雑なパターンや深い加工を必要とする場合、処理時間が更に長くなり、生産効率が低下する傾向にあります。
しかし、この課題に対しては、複数の基板を同時に処理できる大型の浸漬槽を使用したり、自動化システムを導入したりすることで、ある程度の生産性向上が可能です。
また、高精度な加工が要求される特殊部品や、少量多品種生産の場合には、むしろエッチング加工の特性を活かした柔軟な対応が可能となり、競争力のある製造方法として選択されています。
厚板の加工はしにくい
エッチング加工は、薬液の浸透深さに限界があるため、厚い材料の加工には適していません。一般的に、金属板の場合、1mm以上の厚さになると均一な加工が難しくなり、深い溝や貫通穴を作る際には時間がかかったり、寸法精度が低下したりする傾向があります。
しかし、この制限は技術の欠点というよりも、エッチング加工の特性を理解した上で適材適所に使用することが重要です。例えば、厚板の加工が必要な場合は、レーザー加工や機械加工との組み合わせを検討することで、各加工方法の長所を活かした効率的な製造プロセスを構築することができます。
エッチングの処理工程
続いて、エッチングの処理工程を確認していきましょう。
エッチング加工の一連の流れは以下の通りです。
1.フォトマスクの作成
加工したいパターンを描いた原版を作成します。このマスクは光を通す部分と遮る部分があり、これによって後工程でパターンを転写します。
2.エッチング材の処理前洗浄
材料表面の汚れ、酸化膜、油分などを除去し、きれいな状態にします。これにより均一な加工品質を確保します。
3.レジスト塗布
材料表面に感光性樹脂(フォトレジスト)を均一に塗布します。これが後のエッチング工程で保護膜として機能します。
4.露光
フォトマスクを通して紫外線を照射し、レジスト層にパターンを転写します。露光された部分と未露光部分で、レジストの性質が変化します。
5.レジスト除去
露光工程後、現像液を使用して不要なレジストを除去します。これによりパターンが形成されます。
6.エッチング処理
エッチング液に浸漬し、レジストで保護されていない部分を選択的に溶解除去します。
7.硬化レジストの除去
エッチング処理後、残っている保護用のレジストを専用の剥離液で除去します。
8.エッチング後の洗浄
残留したエッチング液や不純物を完全に洗い流し、清浄な表面を得ます。
9.薬液残り対策
最終的な品質確保のため、残留した薬液を完全に除去し、必要に応じて防錆処理などを施します。
これらの工程は連続的に行われ、各工程での品質管理が最終的な加工精度に大きく影響します。
エッチング液の廃液処理方法
ウェットエッチングで重要なのが、エッチング液の処理です。銅のエッチング過程では、塩化銅という有害物質が生成されます。塩化銅の排水に関しては、PRTR法という法律で厳しく制限されており、無害化して下水に流す必要があります。
塩化銅を無害化するための、廃液処理の手順は以下の通りです。
- 消石灰を廃液に投入して水酸化銅と 塩化カルシウムに分解する
- 水酸化銅を加熱して酸化銅と水に分解する
この作業で、有害物質だった塩化銅が、無害な塩化カルシウムと酸化銅にまで分解され、下水に流せるようになります。
またガラスやシリコンに行うウェットエッチングで使われるフッ酸も有害な物質です。フッ酸を無害化するためには、排液に消石灰や塩化カルシウムを混ぜ、無害なフッ化カルシウムを生成させます。
まとめ
エッチング加工は、化学反応を利用した精密な表面加工技術として、半導体製造から芸術作品まで幅広い分野で活用されています。微細加工が可能で変形が少ないという利点がある一方で、厚板加工や大量生産には制約があります。しかし、これらの特性を理解し、適切な用途で活用することで、現代のものづくりに不可欠な加工技術として、今後もさらなる発展が期待されています。
ワールドインテックのFC事業部では、エッチング技術を活かした最先端のものづくりに携わる機会があります。電気自動車やIoT対応の半導体・電子部品製造など、多彩なプロジェクトでスキルを磨きませんか。