半導体におけるエッチングの手法を解説!メリット・デメリットや加工の流れも紹介
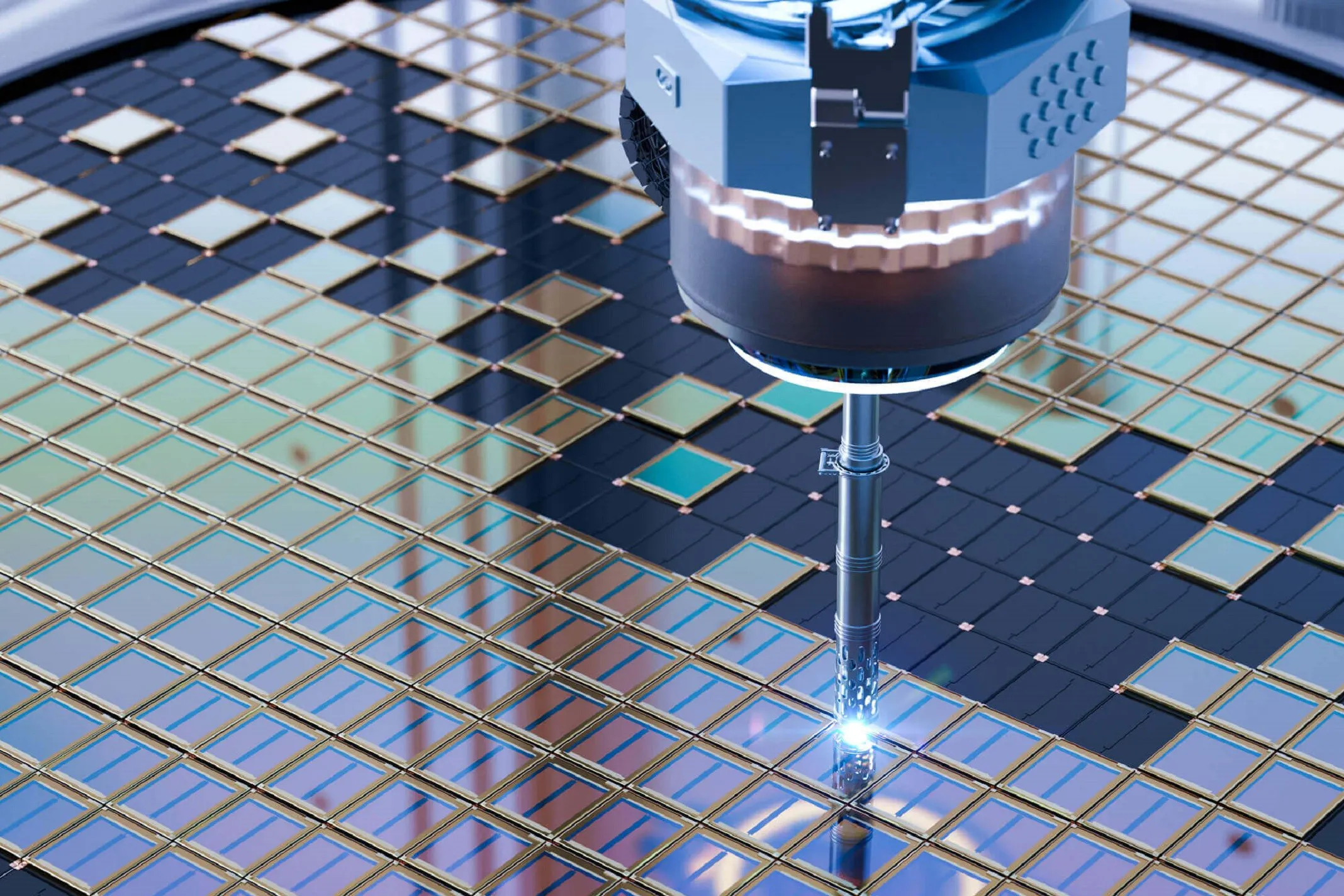
半導体製造において、エッチング技術は欠かせません。しかし、手法の違いやそれぞれのメリット・デメリットを理解しているでしょうか。エッチングの選択は、製品の品質やコストに影響を与えるため、正しく理解することが重要です。
本記事では、ドライエッチングとウェットエッチングの違いや、それぞれのメリット・デメリット、具体的な加工の流れを解説します。また、よくある質問にもお答えし、半導体製造の基本から応用まで理解を深めることが可能です。
この記事を読むことで、半導体エッチングの全体像を把握し、適切な手法を選択できるようになります。製造現場での実践に役立つ知識を身に付け、高品質な製品を作り上げるための参考としてください。
エッチングとは
エッチングとは、金属板や半導体基板の表面に化学反応を利用し、思い通りの模様や回路パターンを彫り込む技術のことです。
半導体製造におけるエッチングでは、ウエハー(基盤)の表面に形成された薄膜(酸化膜など)を化学反応により設計図通りに削り取っていく工程です。保護膜(マスク)で保護された部分は残し、不要な部分を除去することで、ウエハー上に回路パターンを形成していきます。
半導体のエッチングにおける手法は2つ
エッチングには、「ドライエッチング」と「ウェットエッチング」という2つの主な手法があります。それぞれの手法は、異なる特性と用途を持ち、目的に応じて使い分けられます。
ドライエッチング
ドライエッチングとは、真空環境下でガスをプラズマ化し、そのイオンを固体表面に衝突させることで不要な部分を除去する加工プロセスです。イオンが衝突して原子や分子を剥ぎ取る現象を「スパッタリング」と呼びます。
メリットとしては、ウェットエッチングと比べて異方性(エッチングが一方向のみに進むこと)が高く、微細な加工を得意とします。デメリットは、使用するガスや装置が高価であること、ガスの濃度や温度管理など専門的な知識が必要なことなどです。
ドライエッチングの装置は、ナノレベルの緻密な加工や、プラズマによるスパッタリング、設計図通りにエッチングする異方性に対応しています。半導体デバイスの微細化と高集積化を実現するため、重要な役割を果たしています。
ウェットエッチング
ウェットエッチングは、薬液を用いて半導体の表面を化学的に溶解(腐食)させる手法です。ウェットエッチングは、等方性(エッチングが垂直だけでなく水平に進む)の性質から、広範囲の除去や表面洗浄に適しています。
メリットとしては、処理スピードが速いこと、装置のコストが比較的安いことが挙げられます。また、プラズマを使用しないため、基盤へのダメージがドライエッチングより少ないです。デメリットは、加工精度がドライエッチングに比べて劣ること、化学薬品の廃棄処理が必要であることが挙げられます。また、異方性の高い構造の形成には向いていません。
ウェットエッチング装置は、薬液タンク、供給ライン、排液設備などから構成され、薬液洗浄と同様のウェットステーションが利用できます。硫酸、硝酸、りん酸、フッ酸といった薬液の種類を変えることでさまざまな材料に対応可能です。
等方性エッチングと異方性エッチングの違い
等方性エッチングと異方性エッチングは、その材料除去の方向性に違いがあります。
等方性エッチングでは、エッチング反応がすべての方向に均等に進行するため、反応速度は速くなりますが、アンダーカット(横方向での過剰な削り)が発生し、エッジが丸くなってしまいます。異方性エッチングでは、エッチング反応が一方向にのみ進行するため、エッジの立ったパターン形成をできますが、反応速度が遅くなるでしょう。
等方性か異方性かは、エッチングの反応速度によって決まり、エッチング液の濃度、温度、攪拌といった条件によって制御されます。一般的に、強酸を使用すると等方性となり、弱酸を使用すると異方性となるのです。また、エッチング材の結晶構造や結合の強さによっても影響を受けます。
現場では通常、エッジの立ったパターン形成が求められるため、異方性エッチングが好まれますが、反応速度と均一性の両立が課題です。
半導体エッチングの3つのメリット
半導体エッチングの主なメリットは、次の3点です。
初期費用を抑えられる
エッチング加工は金型を必要としないため、初期投資が抑えられます。ウェットエッチングは装置が安価で薬品コストも低く、ドライエッチングは装置が高価であるものの消耗品コストが低いです。
また、メンテナンス費用も少なく、運用コストが低くなっています。工程の自動化も進んでいるため、人的コストも抑えられるでしょう。
特に小ロット・多品種の製造ラインや試作段階では、コストパフォーマンスに優れた加工方法と言えます。
短期間で製造できる
エッチングは処理スピードが速く、短納期で製造できます。ウェットエッチングでは化学反応によりスピーディに加工でき、ドライエッチングでは高度な制御技術で効率化されています。
製品開発の早期化や、市場投入までの期間短縮に貢献する加工方法です。
加工精度が高い
微細な形状にも対応でき、高い加工精度を実現できるのがエッチングの特徴です。ドライエッチングではプラズマを駆使してナノスケールの精密加工が可能です。
また、プロセスパラメータを細かく設定できるため、製品の均一性も保たれ、高品質な製品作りに適しています。
半導体エッチングの2つのデメリット
半導体エッチングの主なデメリットは、次の2点です。
大量生産は難しい
エッチング加工は工数が多く、加工時のコストが高くなるため、大量生産には不向きです。しかし、海外に工場を置いて人件費を抑える工夫をしたり、ロールtoロール方式の大量生産設備を導入したりするなどの対策を取っている企業もあります。
大量生産を依頼する際は、そうした対応力のある加工メーカーを選ぶことが大切です。
厚い板版には対応できない
エッチングは、特に厚い板版の加工には適していません。一般的にエッチングは、薄いフィルムや数ミリメートル程度の厚さの材料を対象としています。厚さが2mmを超える場合、均一な加工が難しくなり、精度が低下します。
これは、エッチング液やプラズマが深部まで浸透しにくいためです。メーカーや素材によっても異なるため、事前に確認しておくといいでしょう。
半導体製造におけるエッチングの流れ
半導体製造におけるエッチングの流れは、以下のとおりです。
- 原版の作成
- 加工する素材の洗浄
- レジストの塗布
- 露光
- レジストの除去
- エッチング
- レジストの剥離・洗浄
- 最終チェック
- STEP 1:原版の作成
設計図に基づいて、ウエハー上に微細なパターンを形成するための原板を作成します。
- STEP 2:加工する素材の洗浄
次に、加工する素材であるウエハーを洗浄します。表面に付着した油分や異物を取り除くためです。異物が残ると回路に異常をきたすため、必要に応じて複数回実施されます。
- STEP 3:レジストの塗布
ウエハーにレジストと呼ばれる感光性の材料を塗布します。レジストは、エッチングプロセス中に保護膜として機能し、特定の領域を保護します。
- STEP 4:露光
原板の上にレジストコーディングした素材を乗せ、紫外線を照射。これで原盤のパターンが転写されます。
- STEP 5:レジストの除去
露光後、不要なレジストを除去し、エッチングする領域をむき出しにします。
- STEP 6:エッチング
エッチングで露出した部分の材料を削り取り、所望のパターンや構造を形成させます。
- STEP 7:レジストの剥離・洗浄
エッチングが完了した後、残ったレジストを剥離し、ウエハーを再度洗浄します。
- STEP 8:最終チェック
最後に品質管理や検査を行い、製品が規格に適合していることを確認します。
半導体エッチングに関するよくある質問
半導体エッチングについて、よくある質問を回答します。
エッチングは半導体以外の分野でも活用できるの?
エッチング技術は、半導体分野だけでなく、さまざまな分野でも活用されています。
以下のような分野で広く使用されています。
- 金属加工
- ガラス加工
- 医療分野
金属素材にフォトリソグラフィによるパターニングを施した後、化学薬品による腐食で加工を行います。リードフレームや電子部品の製造に欠かせません。また、フィルターなどの機能部品や、部品の搬送治具の製作にも多く使われています。
ガラス加工では、フッ化水素などの薬品によりガラスを腐食させ、溝やくぼみを精密に形成することが可能です。マスクパターンを利用するため、ミクロンオーダーの繊細な模様の転写も可能です。そのため、石英ガラスや光学ガラスなどの加工に広く用いられています。
さらに医療分野でも、エッチングの高い加工精度が活かされています。補聴器のフィルターなど、ミクロンサイズの極小穴加工が要求される部品の製造に適しています。バリや歪みの発生が少ないため、人体に直接触れる医療機器部品の製作にも有用な技術なのです。
エッチング加工ができる材料は?
エッチングは腐食性のあるほとんどの材料に適用可能です。
以下のような材料に対して加工が行われます。
- ステンレスや銅などの金属
- シリコン
- ガラス
- セラミックス
金属では、鉄、銅、ステンレス、ニッケル、アルミニウムはもちろん、チタン、モリブデン、タングステンなどの特殊金属も加工対象になります。ウェットエッチングの場合、素材の種類に合わせて適切な薬液を選ぶことで、さまざまな金属素材に対応可能です。
一方、ガラスやセラミックスなどの無機材料もエッチングで加工できます。フッ酸や強アルカリ性の薬品を用いることで、精密なパターン転写が可能となります。
まとめ
この記事では、半導体エッチングの手法、メリット・デメリット、加工の流れについて解説しました。エッチング技術は、半導体製造の重要な工程であり、さまざまな分野で応用されています。
半導体に興味がある方は、ワールドインテックのFC事業部でのキャリアを検討してみてください。FC事業部では、最先端の技術を学びながら、多様な製造現場で経験を積むことができます。400社以上のトップメーカーと取引があり、最新の設備と技術に触れられる環境が整っています。
また、キャリアアップやキャリアチェンジの機会が豊富で、スペシャリストからマネジメント職まで幅広い道が開けています。詳細はこちらからご覧ください。