半導体洗浄の重要性とは?装置の種類・処理方法や特徴をわかりやすく解説
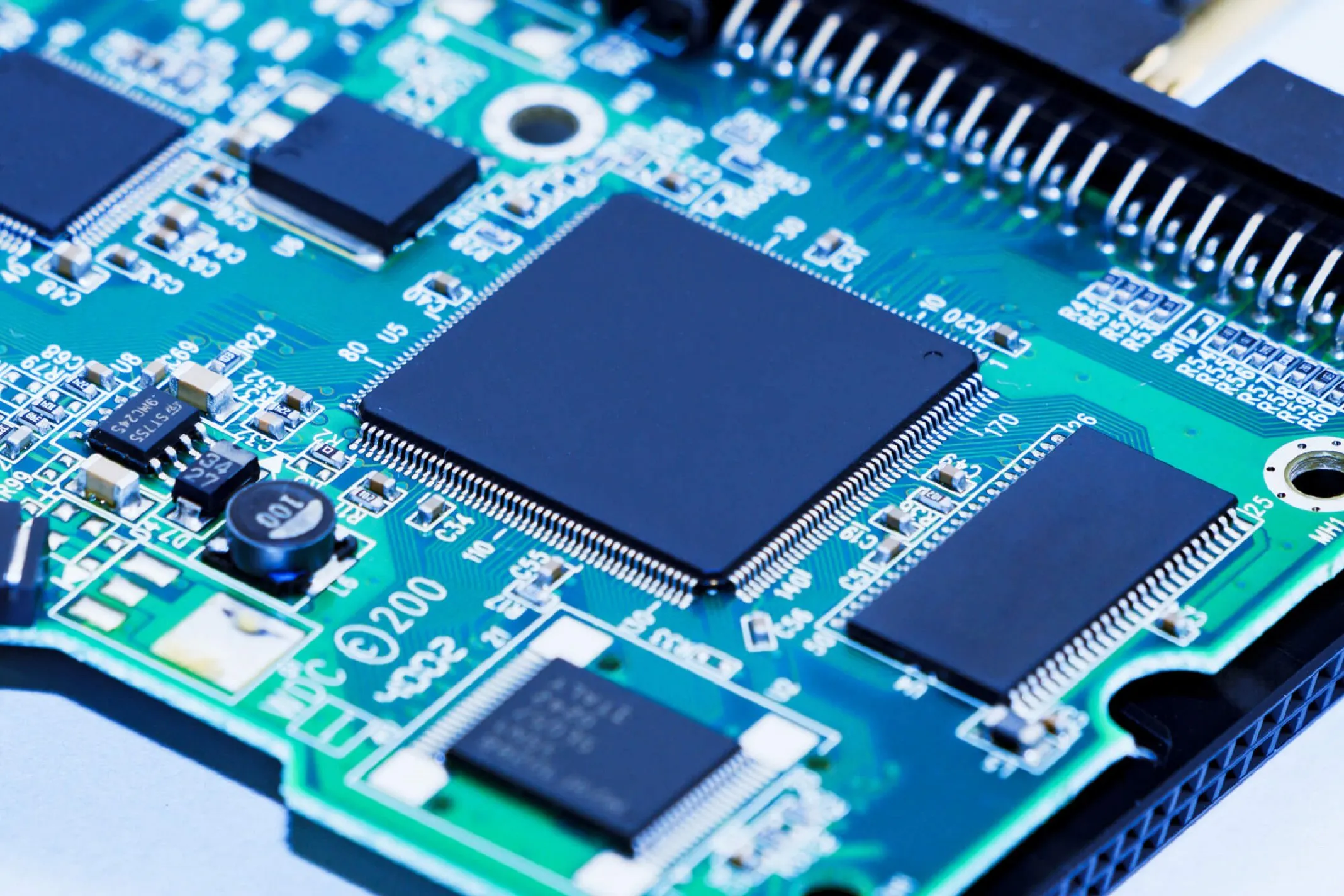
半導体製造において、洗浄工程がどれほど重要か知っていますか。汚染物質が半導体に付着したままだと、品質の低下や製造効率の悪化を招く恐れがあります。半導体の洗浄装置や処理方法にはさまざまな種類があり、ニーズや目的に合わせて最適な手法を選ぶことが大切です。
本記事では、半導体洗浄の重要性、洗浄工程の流れ、洗浄装置の種類、そして洗浄方法について詳しく解説します。半導体洗浄について理解を深めるために最後までご一読ください。
洗浄工程とは
半導体製造における洗浄工程とは、半導体の表面に付着した不要な物質を取り除くことです。「全工程の3割が洗浄工程」と言われるほど、重要な役割を担っています。
不要な物質を除去しないと、半導体の品質や生産性を低下する可能性が高くなります。例えば、パーティクル(微小な塵)が付着していると、配線のショートや絶縁不良などの不具合が発生する可能性があります。また、歩留まり(良品率)を下げることで生産性にも悪影響をもたらすでしょう。
半導体洗浄で除去の対象となる主な物質とその発生源は、以下の通りです。
- パーティクル(空気中を浮遊している塵)
- 有機物(クリーンルーム内の内装材や接着剤、搬送装置などから)
- 金属(搬送装置や薬液などに含まれる重金属から)
- 自然酸化膜(シリコンウエハーが空気に触れて帯びた酸化膜から)
- 油脂(作業員の汗に含まれる脂分や皮脂などから)
こうした物質を確実に除去することで、半導体製品の品質と信頼性を確保できます。
半導体洗浄工程の流れ
半導体の洗浄工程は、半導体の種類によって多少異なりますが、一般的な流れは大きく「設計」「前工程」「後工程」に分かれます。
以下では、設計と前工程について解説します。
1. ウエハー製造
シリコン単結晶(インゴット)からウエハーを薄く切り出す工程です。ウエハー表面・側面を研磨や鏡面化などによって、微粒子や凹凸をクリアにします。
2. 洗浄
ウエハー表面の汚れを除去する工程です。液体や気体の化学薬品を用いた洗浄が行われます。洗浄後のウエハーには微細な汚染物質が残らないよう、非常に高い洗浄度が求められます。
3. 酸化・成膜
洗浄されたウエハー表面に酸化膜や金属膜などの薄膜を形成する工程です。700〜1200度でウエハーを加熱することで、表面に酸化膜が成膜されます。
4. パターン形成
フォトリソグラフィ技術を用いて、ウエハー上に設計図通りの回路パターンを形成する工程です。レジストをウエハーに塗布し、マスクパターンを露光・現像することで、エッチングのマスクパターンが形成されます。
5. エッチング
ウエハー表面の不要な部分を選択的に除去する工程です。ドライエッチングやウェットエッチングなどの方法が用いられます。
6. レジスト剥離・洗浄
エッチング工程後に残ったレジストを完全に除去する工程です。専用の剥離液を用いてレジストを溶解し、さらに洗浄を行うことで、ウエハー表面の汚染を取り除きます。
その後、イオンの注入や表面の研磨、電極の形成を経て、最終的な検査を受けて「設計」と「前工程」は完了です。なお、「後工程」は半導体をウエハーから切り出すプロセスです。
半導体洗浄の詳細な工程や装置の種類、処理方法などにつきましては、こちらの記事を参考にしてください。
【関連記事】半導体の種類について特徴を徹底解説!性質や実生活での活用例も紹介
半導体の洗浄と乾燥は必ずセットで行う
半導体製造における洗浄工程では、洗浄と乾燥は必ずセットで行われます。「ドライイン・ドライアウト」とも言います。セットにする理由は、洗浄後にウエハー表面に水分が残されていると、さまざまな問題が生じるからです。
薬液などの水分が付着したままだと、ウエハー表面で酸化が起きたり、斑点(ウォーターマーク)ができたりします。さらに、後工程で水分が残っていると、ウエハーが劣化したり欠陥が生じたりする可能性もあるでしょう。
このように洗浄だけでは製品不良のリスクを排除しきれないため、洗浄と乾燥は必ずセットで行わなければなりません。
半導体の洗浄装置の種類
半導体の洗浄には、さまざまな種類の専用装置が用いられています。
3つの代表的な装置について解説します。
- 多槽バッチ式
- 単槽バッチ式
- 枚葉式
多槽バッチ式
多槽バッチ式の装置は、いくつもの専用槽に異なる薬液を入れ、ロボットがウエハーをそれぞれの槽に移し替えながら段階的に洗浄していく方式です。
多槽バッチ式は、複数のウエハーを同時に処理できるため、スループット(時間ごとの処理能力)が高いです。しかしながら、装置の床面積が大きくなり、薬液や純水を大量に消費するというデメリットがあります。
ロボットの搬送方法として「ウエハーキャリア(専用カゴ)」を使用する場合、さらに装置が大型化します。一方、「キャリアレスタイプ」を選んだ場合は、ウエハーをつかむ搬送チャックを石英ガラスなどにする必要がありコストがかかるでしょう。
単槽バッチ式
単槽バッチ式は、1つの槽で複数の工程を行う方式です。単槽バッチ式には、「ディップ式(処理槽に浸す方式)」と「スプレー式(薬液をウエハーに吹きかける方式)」があります。
処理槽が1つしかないため、装置の床面積を小さくできます。薬液を送る配管や使用済みの薬液を排出する配管のレイアウトが複雑になるため、装置の製造コストが高くなってしまうという欠点があります。
また、ディップ式ではパーティクルの再付着が起こりやすく、スプレー式では薬液の回収が難しいという課題もあります。
枚葉式
枚葉式は、ウエハーを一枚ずつ処理するスプレー式です。洗浄面を水平方向に回転させながら、ノズルで薬液を吹きかけます。
装置の構造がシンプルで小型化できるため、コストとクリーンルームのスペースを削減できます。また、パーティクルの再付着がなく、薬液使用量も少なくて済みます。
一方で、スループットがバッチ式に比べて劣り、薬液の回収と配管が複雑になるというデメリットがあります。
半導体洗浄の処理方法
半導体の洗浄は、処理方法によってやり方や特徴が異なります。一般的なのはウェット式ですが、ドライ式も利用されています。
ウェット式
ウェット式は液体を用いて洗浄を行う方法です。薬液につけ置きしたり(多槽バッチ式、単槽バッチ式)、スプレーで液を噴射したり(枚葉式)と、さまざまな手法があります。
ウエハーを専用の「ウェットステーション」に設置して行うのが一般的です。ウェットステーションには、複数の薬液タンクと各種ノズル、排水設備などが備わっています。薬液を切り替えながらウエハーを処理していきます。
ウェット式のメリットは、液体を扱うので作業が容易なことです。一方で、薬液の表面張力によりウェハーの微細構造にダメージを与えるリスクがあります。また、大量の薬液と純水を必要とするため、コスト面でのデメリットもあります。
ドライ式
ドライ式は液体を使わずに乾式で洗浄を行う方法です。さまざまな手法がありますが、代表的なものが「スピン乾燥」と「IPA乾燥」です。
スピン乾燥は、ウエハーを高速回転させ、遠心力で水分を振り払うものです。IPA乾燥は、水より揮発性の高いイソプロピルアルコール(IPA)に置き換えるものです。
ドライ洗浄はガスを反応剤として用います。薬液を使わないため、表面張力によるダメージを心配する必要がありません。また、薬液や純水の使用量が少なくて済むメリットがあります。
一方で、ガス分子の密度が低いため、化学反応が緩慢になりがちです。そのため、高温化などの対策が欠かせず、プロセスが複雑化するデメリットがあります。さらに、反応の制御が難しく、ウエハー表面に損傷を与える可能性もあります。
まとめ
半導体製造における洗浄工程は、製品の品質と生産性を確保するために欠かせないプロセスです。微細な汚染物質を除去することで、信頼性の高い半導体製品が生産されます。
半導体に興味がある方は、ワールドインテックのFC事業部でのキャリアを検討してみてください。FC事業部では、最先端の技術を学びながら、多様な製造現場で経験を積むことができます。400社以上のトップメーカーと取引があり、最新の設備と技術に触れられる環境が整っています。
また、キャリアアップやキャリアチェンジの機会が豊富で、スペシャリストからマネジメント職まで幅広い道が開けています。詳細はこちらからご覧ください。