半導体の製造工程を大公開!働く際の注意事項についても解説
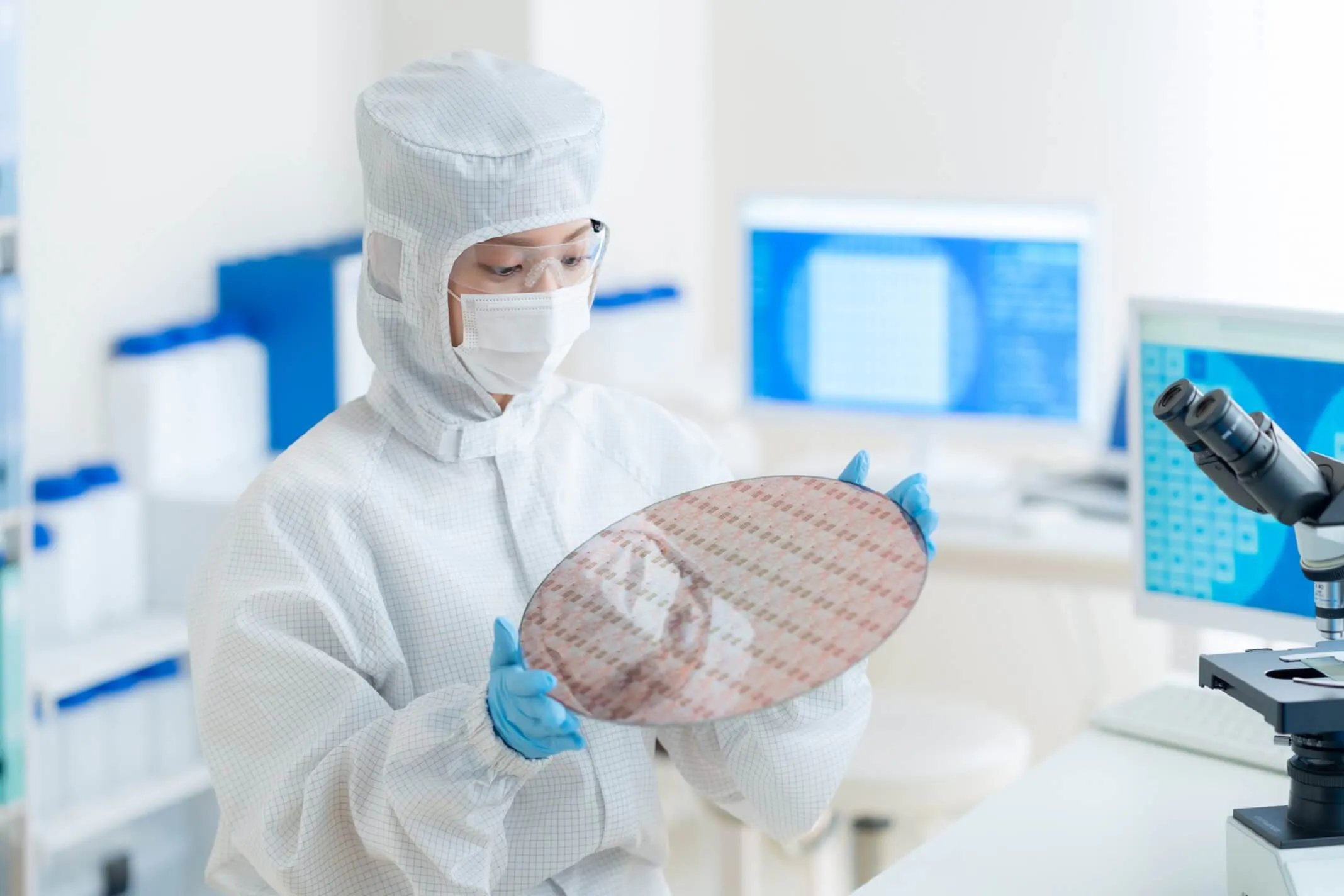
私たちが日常的に使用している電子機器には、必ずと言っていいほど半導体が使われています。
しかし、この重要な半導体がどのように作られているのか、その製造工程について詳しく知っている人は意外と少ないのではないでしょうか。
この記事では、半導体の製造工程について、その全体像や作業時の注意点などを初心者の方にもわかりやすく解説します。
【関連記事】半導体とは?定義や仕組みをわかりやすく解説!3つの役割や日常生活での使用例も紹介
半導体の製造工程
半導体の製造工程は、大きく分類すると「設計」「前工程」「後工程」の3つがあり、これらの工程が組み合わさって、高性能な半導体が生み出されています。
- 設計:半導体の設計図を作る工程
- 前工程:シリコンウェーハに回路を作り込む工程
- 後工程:個々のチップに分割して組み立て、製品として完成させる工程
それぞれの工程について詳しく解説します。
設計
設計工程は、半導体の性能と品質を決定づける重要な段階です。この工程では、コンピュータを使って緻密な計算とシミュレーションを繰り返し、最適な回路パターンを決定していきます。
設計は主に以下の2つの工程で進められます。
- 回路・パターン設計
- フォトマスク作成
各工程の具体的な作業内容を紹介します。
回路・パターン設計
回路・パターン設計は、半導体に必要な機能を実現するための基本的な回路構成を決める工程です。
また、その回路をどのように配置すれば最も効率的に動作するか、コンピュータを使ってさまざまなパターンをシミュレーションします。この際、消費電力や発熱、信号の伝達速度といった要素も考慮しながら配置を検討していきます。
フォトマスク作成
回路パターンが決定したら、それを透明なガラス板に描き写して「フォトマスク」を作成します。フォトマスクは、後の工程でシリコンウェーハに回路を転写する際の原版となる重要な部材です。
ナノメートル単位のパターンを正確に描く必要があるため、高精度の電子ビーム描画装置を使用します。
前工程
前工程とは、シリコンウェーハと呼ばれる円盤状の基板に、実際の電子回路を形成していく工程です。この工程では、ナノメートル単位での加工が求められ、最先端の技術とクリーンな環境が必要です。
前工程は以下の手順で進められます。
- シリコンインゴットの切断
- ウェーハの研磨
- ウェーハ表面の酸化
- 薄膜の形成
- フォトレジストの塗布
- 露光・現像
- エッチング
- レジストの剥離・洗浄
- イオンの注入
- ウェーハ表面の平坦化
- 電極の形成
- ウェーハの検査
特に「フォトレジストの塗布」から「ウェーハ表面の平坦化」までの工程を何度も繰り返し行うことで、複雑な回路が形成されていきます。
1.シリコンインゴットの切断
シリコンの純度を高めた円柱状の結晶(インゴット)を、ダイヤモンドワイヤーを使って薄く切断します。
切断されたシリコンの円盤は「ウェーハ」と呼ばれ、このウェーハ1枚から数百個の半導体チップを作ることができます。
2.ウェーハの研磨
切断工程で生じた表面の凹凸を取り除くため、特殊な研磨剤とパッドを使ってウェーハを磨き上げます。ナノメートル単位で研磨を行うことで、ウェーハの表面は鏡のような滑らかさになります。
3.ウェーハ表面の酸化
研磨されたウェーハを高温の酸素にさらし、表面に二酸化シリコンの膜(酸化膜)を形成します。この酸化膜は電気を通しにくい性質を持ち、トランジスタの絶縁層として重要な役割を果たします。
4.薄膜の形成
酸化膜の上に、さまざまな材料の薄い膜を形成していきます。
主な方法としてCVDとスパッタリングがあります。CVDは、原料となる気体を高温で分解し、化学反応によって膜を形成する方法です。
一方のスパッタリングは、材料をイオン化して基板に吹き付けることで膜を作ります。
5.フォトレジストの塗布
ウェーハの表面全体に感光剤(フォトレジスト)を均一に塗布します。フォトレジストは光が当たると化学変化を起こす特殊な物質で、回路パターンを形成する際の型として使用されます。ウェーハを高速で回転させる遠心力により、ナノメートル単位の均一な厚さで塗ることが可能です。
なお、使用するフォトレジストには、光が当たった部分が溶ける「ポジ型」と、光が当たっていない部分が溶ける「ネガ型」の2種類があり、作る回路の特性に応じて使い分けられます。
6.露光・現像
フォトマスクを通して紫外線をウェーハに照射し、回路パターンを転写します。
フォトマスクには、先の工程で作られた回路パターンが描かれており、このパターンに合わせて光を照射することで、ウェーハ上のフォトレジストに回路の形が焼き付けられます。
その後、現像液を使ってフォトレジストの特定部分を溶かし出すことで、ウェーハ上に回路パターンが形成される仕組みです。
7.エッチング
フォトレジストで保護されていない部分の薄膜を、化学薬品やガスを使って除去します。
エッチングの方法には、薬液を使用するウェットエッチングと、ガスを使用するドライエッチングがあり、形成する回路の特性に応じて使い分けられます。
8.レジストの剥離・洗浄
エッチングが完了したら、残っているフォトレジストを専用の剥離液で除去します。その後、超純水や特殊な洗浄液を使って洗浄し、ウェーハ表面に付着した不純物や残留物を完全に取り除きます。
9.イオンの注入
半導体の電気的特性を制御するため、特定の不純物(ドーパント)を高速で打ち込みます。イオン注入装置の使用により、不純物の量と深さを原子レベルで精密にコントロールすることが可能です。
注入後は熱処理を行い、結晶構造の修復と不純物の活性化を行います。
10.ウェーハ表面の平坦化
ウェーハ表面の凹凸を研磨して平らにします。表面をきれいにした後、あらためて次の層の形成を始めます。
「フォトレジストの塗布」から、この「ウェーハ表面の平坦化」までの工程を何度も繰り返し、必要な回路を作り込んでいきます。
11.電極の形成
すべての層を形成し終えたら、回路と外部を接続するための電極を形成していきます。
絶縁層として働く酸化膜にコンタクトホールと呼ばれる小さな穴を開け、穴に配線用の金属を埋め込みます。金属が埋め込まれることで、チップ内部と外部を接続するための電気の通り道ができます。
12.ウェーハの検査
シリコンウェーハ上に作られたすべてのチップの品質検査を行います。プローブと呼ばれる極めて細い針を使って、一つ一つのチップの電気的な動作確認を実施します。
この検査は、動作確認に加えて、表面のキズや汚れ、チップのサイズといった外観に問題がないかも入念にチェックする前工程の最終段階です。
後工程
後工程は、半導体チップを実用的な製品として完成させるための工程です。
前工程で作られたウェーハから個々のチップを切り出し、保護や配線を施して製品化していきます。チップは非常に小さく繊細なため、静電気や衝撃による損傷を防ぎながら、慎重に作業を進めることが重要です。
後工程は以下の手順で行われます。
- ダイシング
- ワイヤーボンディング
- モールディング
- 最終検査
1.ダイシング
前工程で作られたシリコンウェーハには、数百個もの半導体チップが並んでいます。ダイシング工程では、このウェーハをダイヤモンドブレードという特殊な刃を使って、一つひとつのチップに切り分けていきます。
2.ワイヤーボンディング
切り分けられたチップをリードフレームと呼ばれる金属の枠に取り付け、チップとリードフレームを細い金線でつないでいきます。この配線作業により、チップと外部機器との電気的な接続できるようになります。
3.モールディング
配線が済んだチップを樹脂やセラミックで包み込みます。モールディングは、繊細な機器であるチップを、キズや衝撃、ホコリ、磁気といった外部の影響から保護するための工程です。
4.最終検査
製品として出荷する前に最終的な品質確認を行います。温度を変えた環境での動作テストや、電圧をかけての性能確認など、さまざまな角度から検査を実施し、製品に求められるすべての基準を満たしたものだけが出荷されます。
半導体の製造工程に関わる際の注意事項
半導体の製造には、ナノメートル単位の技術が必要とされます。
そのため、製造に関わる際は、特に以下の点に注意が必要です。
- 高精度・高品質を意識して作業する
- 身だしなみを整える
高精度・高品質を意識して作業する
半導体製造では、ナノメートル単位の精密な作業が求められます。わずかなズレが製品の欠陥につながってしまうため、常に作業へ集中することが大切です。
また、製造装置の設定や調整、材料の取り扱いに細心の注意を払い、わずかな変動も見逃さない注意深さも求められます。
自分が担当する工程が製品全体の品質に影響を与えることを理解し、責任を持って作業に取り組むようにしましょう。
身だしなみを整える
半導体は繊細な精密機器です。わずかな汚れやキズでも製品の品質に影響を与える可能性があるため、製造現場では清潔な環境を保つことが極めて重要です。
そのため、半導体工場では厳密な環境管理が行われていますが、作業者自身の身だしなみや清潔さも同様に重要な要素となります。作業者一人ひとりが清潔な状態を保ち、適切な服装で作業に臨むことで、製品の品質が保たれます。
製造現場のルールを守り、製造環境に相応しい状態で作業に取り組むことを心がけましょう。
半導体製造工程に関するよくある質問
最先端の技術が集約されている半導体製造は、多くの人が関心を持っている分野だといえるでしょう。
ここでは、半導体製造についてよくある質問にお答えします。
半導体業界の将来性は?
私たちの生活に欠かせないデジタル機器の基幹部品として、半導体の需要は年々拡大しています。特に、自動車の電動化やIoTの普及、5G通信の展開により、半導体の需要は今後さらに増加すると予測されています。
また、AI(人工知能)やビッグデータ処理といった新しい技術の発展に伴い、より高性能な半導体へのニーズも高まっています。そのため、半導体業界は長期的な成長が期待される分野だといえるでしょう。
技術革新のスピードが速く、常に新しい知識や技術の習得が求められる一方で、人々の生活を支えるやりがいのある仕事としても注目を集めています。
【関連記事】半導体不足はなぜ解消しないの?原因や影響、いつまで続くのか を解説
半導体製造で有名なメーカーは?
半導体製造装置で有名なメーカーとしては、東京エレクトロンやScreenなどが挙げられます。
東京エレクトロンは、コータ・デベロッパーや成膜装置、洗浄装置など、幅広い装置でトップクラスのシェアを誇っており、Screenは表面処理技術や直接描画技術に強みがあります。
しかし、世界市場全体で見ると、アメリカやオランダの企業が大きなシェアを占めているのが現状です。日本企業の技術力は高く評価されているものの、グローバル市場ではさらなる成長が期待される状況となっています。
【関連記事】半導体製造装置とは?製造業界のシェア率やメーカー、部品の特徴や種類を解説
まとめ
半導体の製造工程は、「設計」「前工程」「後工程」という3つの大きな工程に分かれています。
設計工程で製品の性能を決定づける回路パターンが作られ、前工程でシリコンウェーハに実際の回路が形成され、後工程で製品として完成に至ります。
どの工程においても高度な技術と細心の注意が必要とされる半導体製造ですが、私たちの生活に欠かせない重要な産業として、今後もさらなる発展が期待されている分野です。製造に携わる人々には高い技術力と品質への意識が求められますが、それだけにやりがいのある仕事だといえるでしょう。
ワールドインテックのFC事業部では、半導体関連の仕事に携われます。最先端の製造技術を学びながら、自分らしいキャリアを築ける環境が整っているため、半導体の製造に興味がある方は、ぜひ一度検討してみてはいかがでしょうか。